Optical Metrology
Optical metrology methodologies and nondestructive testing (NDT) have been utilized for measurement of shapes, deformations, residual stresses, impact dynamic analyses, mechanical characterization, and structural health monitoring for different applications ranging from aerospace and automation to health and energy. They enable the characterization of mechanical properties, shape, and geometrical distortions, as well as porosity and defect. For instance, applied dynamic and controlled vibration using non-invasive optical methods are employed to evaluate components’ performance and characteristics. These methods are capable of non-invasively and accurately assessing some mechanical and structural properties such as moduli of elasticity, damping coefficient, stiffness, shear moduli, and Poisson’s ratio. Additionally, this analysis provides information about inhomogeneity and defects in the structure.

Fig. 1. The representative images of the four main optical non-destructive sensors that were utilized: (a) Thermography to measure the temperature; (b) Digital Holography to measure the natural frequency and mode shape in full-field-of-view; (c) Impact analyses using Digital Image Correlation (DIC); (4) Digital Fringe Projection to measure the shape and curvature of the printed samples. Source: K.P. Dissertation
Thermography and thermal imaging
Thermography offers full-field-of-view, non-contact, and non-invasive measurements. These superior capabilities make thermography one of the most widely used sensors in monitoring and closed-loop control systems in AM technologies. However, the thermal measurement can only measure surface temperature and is very sensitive to environmental fluctuations. Another issue is that accurate measurement requires a reliable understanding of the material properties such as emissivity and absorptivity.
IR camera shows promising potential in FDM processes due to the less harsh environment inside the machine.
In-situ thermography of cylinders printed by FDM , Source: K.P. Dissertation
In-Situ thermal imaging of an artifact printed by FDM, Source: K.P. Dissertation
Shape and distortion measurements
There are different optical methods capable of measuring shape and distortion. Among them are Digital Holographic Interferometry (DHI), Digital Image Correlation (DIC), and Digital Fringe Projection (DFP). These methods have several merits in comparison to other available methods such as ease of use, rapid full-field-of-view measurement, modular design, high accuracy, and flexibility. These methods can also characterize mechanical properties, shape, geometrical distortions, and porosity and identify defects.
DIC is a non-contact method that by tracking the random pattern on the surface of an object, measures the displacement of the Area Of Interest (AOI). The patterns must have enough contrast to be registered by the camera's sensor and may be printed, painted, or already existing as natural features of the AOI. DFP, broadly categorized under structural light modulation, relies on trigonometry by measuring the deformed shape of a binary or sinusoidal intensity profile that is projected on the area of interest. Out-of-plane information of the object is encoded into images recorded by the acquisition sensor.
Time-average DHI was used for measurement of the vibration modes and natural frequencies of specimens. A coherent light source is divided into two beams: (1) the intact beam (called the “reference beam”) directly impinges a light-sensitive sensor; and (2) the second beam (called the “object beam”), covers the object of interest and produces a reflection that reunites with the reference beam on the sensor. These two beams interfere and form bands of bright and dark intensity showing the constructive and destructive interferences of the two beams called fringes. In time-average techniques, the imaging tool captures the interference during a window larger than the vibration period, and the fringes that form on the sensor illustrates the amplitude of vibration.
Digital Holographic Interferometry (DHI)
A type of setup for time-average DHI, optical head, and the schematic labeling the components are illustrated in Fig. 2. Such a setup consists of a solid-state electrically pumped diode laser with a wavelength of 532nm.
The laser beam divided into two beams, one of which, object beam, is reflected by mirrors to illuminate the AOI in the XY plane with a 40x beam expander. This expander diverges the object beam to cover the sample thoroughly. The object beam also passes through a spatial filter to provide a smooth Gaussian distribution to enhance fringes' quality. The second beam called the reference beam is coupled into a fiber and goes to the optical head where it meets the collected reflected object beam off the surface of the object of interest. These two beams interfere on the sensor of the CCD camera.

Fig. 2 Digital holographic interferometric setup sensitive to out-of-plane displacement: (a) DHI setup: BS represents beam splitter; M1, mirror; PZT, piezo for phase stepping; DL1 and DL2, beam expanders; SF1, spatial filter; OB and RF, object beam and reference beam; FI, fiber; CP, fiber coupler; and CCD, video camera; and (b) The setup in operation with a close view of the optical head. Source: K.P. Dissertation
Cameras and the PZT were connected to a DAQ and computer platform for synchronization required for the 4-phase stepping algorithm. The digital CCD camera recording images that are analyzed later for extracting the mode shape and natural frequencies. such a mode shape and their comparison with Finite Element Analyses are shown in Fig. 3.
Digital Image Correlation (DIC)
Digital Image Correlation (DIC) is also one of the widely used non-destructive method for a wide range of application. It can be employed in tandem with high-speed cameras to capture the impact or rapture mechanism. Such a setup designed for impact analyses is shown in Fig. 3. An impact mechanism as simple as a pendulum or drop mechanism can exert impact to specimens. This load initiates a transient responses in the specimens to be capture using Photran SA-Z cameras with the temporal resolution of a maximum of 2 million frames per second and later the images be analyzed using DIC for extracting meaningful data pointing out to the mechanical properties of interest such as module of elasticity and damping coefficient. The schematic and the picture of the setups are shown in Fig. 3.

Fig. 3. Digital image correlation for impact analyses on the printed specimens: (a) Schematic of the stereo 3D DIC; and (b) the drop-impact setup for transient analyses on the printed artifacts 2D DIC. Source: K.P. Dissertation
DIC is a commercially available software package and Correlated Solutions, GOM, and Trilion are among the well-designed and reliable packages out there. General and more technical information about DIC can be found in the supplier websites and in digitalimagecorrelation.org.
Vertical Displacement measured by DIC, Source: K.P. Dissertation
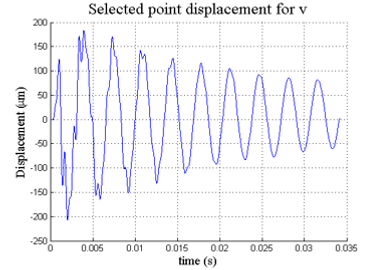
Fig. 4. Vertical Displacement measured by DIC at the tip of the bar shown in top video, Source: K.P. Dissertation
Horizontal Displacement measured by DIC, Source: K.P. Dissertation
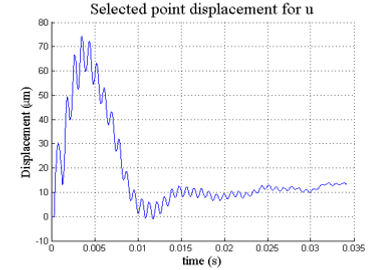
Fig. 4. Vertical Displacement measured by DIC at the tip of the bar shown in top video, Source: K.P. Dissertation