What is 3D printing?
AM is a revolutionizing manufacturing processes that fabricates 3D object directly from a 3D solid file by selective deposition of the material. ASTM Committee F42T agreed to name this category of manufacturing “Additive Manufacturing (AM)” as opposed to subtractive manufacturing [ASTM F2792-12a]. There are several aliases that all refer to AM, i.e., additive fabrication, additive processes, additive techniques, additive layer manufacturing, layer manufacturing, Free Form Fabrication (FFF), solid freeform fabrication, rapid prototyping, and 3D printing that all refer to the process of joining material layer-upon-layer to realize a part consecutively and controllably according to a predefined slicing of a 3D digital file. The following figure shows the three main steps of converting a 3D solid part into a real object.
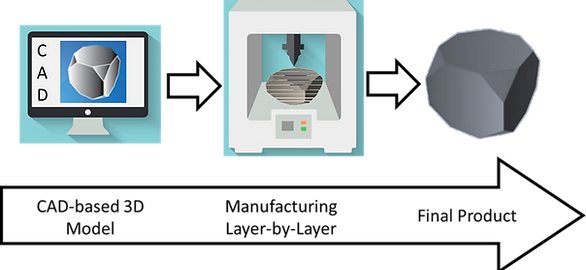
Overview of the process of additive manufacturing starts with the realization of a 3D digitalized file, deposition of the material selectively layer-upon-layer, and post-processing to prepare the final product.
There has been tremendous progress in the past decades that promotes the emerging AM as a potentially disruptive technology. However, AM is not going to supplant subtractive manufacturing in mass production, low material cost, capital investment, speed, and centralized manufacturing at least in the near future. Customization, optimization, sustainability, design freedom, flexibility, energy efficiency, and limitless creation are a few merits of AM technology to accelerate its adoption worldwide. Additionally, this growing interest could reduce cost, energy consumption, and carbon emission sooner than ever.
​


Photo by ThisIsEngineering from Pexels
Photo by Oak Ridge National Lab from Flikrc

Photo by ZEISS Microscopy from Flikrc
Design freedom and optimization incorporated with the possibility to print functionally graded material gives the AM incredible advantages over conventional manufacturing to fabricate intricate and complex shapes that are accessible with no or little tooling. The product can be designed for manufacturing with fewer concerns about its manufacturability and more focus on customizability and functionality. Complexity is a trade-off in conventional manufacturing whereas AM this is not a significant factor, and AM shifted the design paradigm to limitless creation and innovation.
​
The classes of materials that are able to be manufactured by AM include metals, ceramics, polymers, composites, and biological substances. Although the technology initially started with polymer-based materials, it sharply shifted toward metallic materials, and soon a wide variety of technologies become available that fabricate parts with high quality and viable application. The first commercially viable machine was Stereolithography (SLA) using photopolymers manufactured in the U.S. by a company named 3D System in 1986. The next giant leap took place with a technique called Fused Deposition Modeling (FDM) which was commercialized by Stratasys.

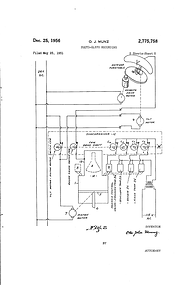
However, even before these two distinguished breakthroughs the technology that was based on the layer-wise manufacturing by exposure of layers of transparent photo emulsion was introduced in a patent in 1951 being called “Photo-glyph”.
Photo by Patent.Google.com
Additive manufacturing and 3D printing technologies
According to the American Society for Testing and Materials, ASTM, additive manufacturing is classified to 7 main categories:
(1) binder jetting,
(2) directed energy deposition,
(3) material extrusion,
(4) material jetting,
(6) sheet lamination, and
All these techniques share the common steps, which start with a product idea and a digital watertight 3D file, that slicing software used to divide it into thousands of layers according to the printer resolutions or selected layer thicknesses. Each layer is a cross-section of the part on that specific location with the selected thickness. Finally, different sources of energy like laser, electric beam, plasma, extruder, ultrasonic, heating elements, electric arc are used for deposition of the material on each layer sequentially from the very first to the last spot on the last layer. The following pages briefly described a few well-known 3D printing technologies including powder bed, energy deposition, polymerization, and material extrusion.

The flowchart shows the process of converting an idea to actual components based on AM