What is Binder Jetting Process?
This technology is firstly introduced back in 1993 by the Massachusetts Institute of Technology (MIT), when an inkjet-based process is devised to form three-dimensional objects by joining metal powders layer-by-layer.
​
In its early days due to the license agreement, only one company names Extrude Hone Corporation was working to commercialize this technology. ExOne.com, one of the key role players in the market right now is spun off from Extrude Hone Corporation.
The original patents expired in 2010 and since then several other companies start working on commercializing binder jetting technologies such as Voxeljet, Digital Metal, HP, and 3DEO. The outcome of license expiration expands the market share of this technology and innovation drives the progress toward reliable binder jet AM machines available in the market right now.
​
Binder jetting resembles Powder Bed Technologies in scanning and powder spreading. The main difference is the consolidation process. A liquid polymer, as shown in Fig. 1, is used instead of a laser or electron beam to shape a primitive structure called a green structure. In this case, the powder is aggregated due to the weak bonding of the polymer. These green parts are later placed in an oven to complete the sintering processes after the scanning is finished. In the oven, bonding polymers are vaporized leaving the sintered powder behind in a final shape. The variety of materials available in binder jetting ranges from ceramic, foundry sand, and polymer, and metal powders.
​
Binder jetting technology demonstrated its capability to print parts precisely with their mechanical properties to be comparable to those printed with other technologies like powder bed fusion or DED or even with traditionally manufactured metal components.
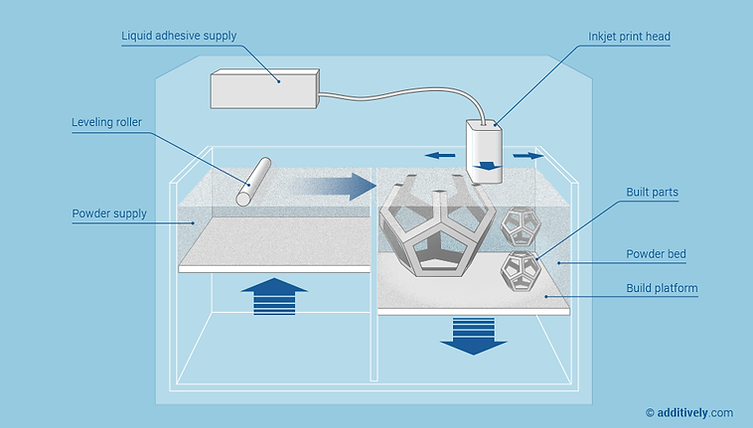
Fig. 1. Binding jetting technology for manufacturing ceramic, metal, and polymer using powder and liquid binder, the system consists of liquid binder supply, inkjet printhead, build platform, powder supply system, and powder leveling system. [51] (image from additively.com)
Metal Binder Jetting, Source: ExOne.com
Ceramic Binder Jetting, Source: Voxeljet.com
Binder Jetting Pros and Cons
Pros:
(1) Fast, lead to higher volumetric outcomes,
(2) High precise,
(3) Little to no residual stress, or thermal related defects compared to DED or SLM
(4) No need for support structures,
(5) Affordable compared to DED or SLM,
(6) Full-color option printing.
Cons:
(1) Essential post-processing steps such as curing, sintering, and infiltration,
(2) Achieving high strength 3D printed component requires elaborate process optimization and post-processing efforts,
(3) Shrinkage because of sintering can lead to size and features inconformity.
​
Who makes Binder Jetting machines
ExOne has introduced different systems to the market so far, and it is the first company that makes Binder Jetting machines commercially available.
​
Digital Metal was founded in 2012 and since then introduced several machines to the market. A fully automated Binder Jetting machine is Digital Metal's innovative solution that makes its way to the market in 2019.
​
HP is a relative newcomer to this market; HP's Binder Jetting machine named Metal Jet is introduced in 2018. Since the concept of inkjet printing is so familiar to HP, it should not surprise anyone that HP was able to innovate and market its products aggressively.
​